
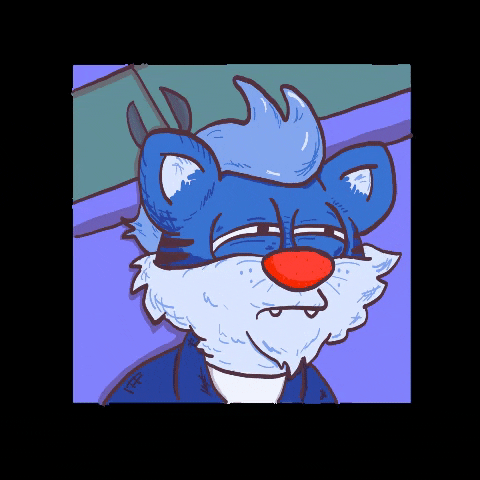
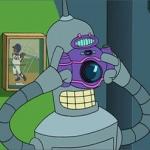
However, for production parts, spares, and repairs, the industry requires a set of unified standards to reduce the costly one-off qualification needed for each AM technology, and, in many cases, each individual application produced. For non-production applications, such as prototypes or some manufacturing aids, AM is an attractive alternative to traditional processes. However, this is evolving, and we are beginning to see more college classrooms introducing metal additive curriculums.įinally, there is the challenge of qualification. AM is still in its infancy, so the tribal knowledge associated with this technology makes it tough to learn and adopt. Depending on who you ask, the casting industry dates to 3300–4000 BC, so it’s obvious that we’ve learned a few things during that time. There are many factors, but part cost is just too high to create a compelling case. The need for secondary processes to finish parts, such as Hot Isostatic Pressing (HIP), also adds cost to the bottom line. Raw materials, such as metal powders, are not only costly but can be difficult to procure and challenging to handle.
#Bender neat image driver#
Throughput rates are the number one driver of cost and currently most metal AM technologies are just too slow. Simply put, metal Additive Manufacturing is just too expensive to replace conventional processes like high-speed machining, sheet metal forming and casting.
